JLR Unveils Ambitious £100M Plan to Revolutionize EV Parts
- Hanaa Siddiqi
- 6 hours ago
- 2 min read
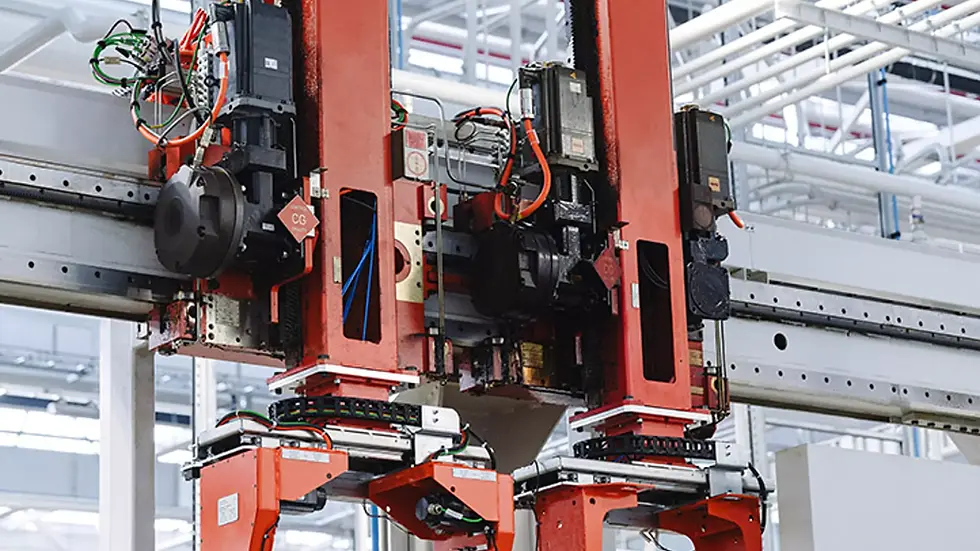
In a strategic move to reduce waste and foster sustainability, Jaguar Land Rover (JLR) has announced an ambitious £100 million investment plan to recycle, repurpose, and reuse metal, robotics, and manufacturing kits from its production sites. This initiative is a step toward the company’s vision of a circular economy designed to enhance the efficiency and sustainability of its operations.
At the heart of this effort lies the Castle Bromwich facility, which ceased production last year yet remains a hub of resourcefulness. Over 50,000 square meters of production equipment—from entire production lines to humble screwdrivers—have been salvaged and redistributed across JLR's UK facilities and to their sites in Nitra and Slovakia.
But that’s not all. More than 18,600 tonnes of scrap metal from these plants have found new life through recycling and sent to suppliers to be processed and reused. This move recycles vital materials and reduces JLR's environmental footprint. The impact? Over 1,200kg of CO2e emissions are avoided for every tonne of steel recycled.
JLR’s chief sustainability officer, Andrea Debbane, said: “As we are entering a critical phase in our electrification journey, JLR has at heart and aims to act as a responsible user of resources by enhancing product utility and longevity and maximising recycling and repurposing.
“It’s not only the right thing to do but also improves profitability and increases supply chain resilience. Through these initiatives, JLR advocates that sustainable choices are not always more expensive; they can help reduce costs and even become opportunities for the growth and development of our colleagues.”
JLR’s dedication to sustainability also extends to its robotics, with hundreds of robots being refurbished and relocated to key locations like Solihull, Halewood, and the Electric Propulsion Manufacturing Centre (EPMC) in Wolverhampton. These robots are now integral to developing the company’s electric vehicles (EVs) and batteries—key components in JLR’s transition to a greener future.
A pioneering digital asset management system has also been introduced. Developed in-house, this system ensures the efficient tracking and management of assets, from their acquisition and use to their eventual recycling or reuse, supporting JLR’s efforts to keep valuable resources in circulation.
This push for sustainability is closely aligned with JLR’s overarching strategy to build the next generation of EVs at its UK-based facilities. Earlier this year, the company also announced a £65 million investment aimed at enhancing its special paint facilities worldwide. With a strong focus on reducing the environmental impact of what is traditionally one of the most carbon-intensive processes in automotive manufacturing, JLR is making strides in adopting sustainable technologies.
The upgrades include energy-efficient paint booths, automated spray robots, and electric curing ovens. Smart heat recovery systems will also be integrated to lower carbon emissions, reduce water consumption, and optimise energy efficiency while maintaining high production capacity.
With these efforts, JLR is investing in the future of automotive technology and in a greener, more sustainable manufacturing process—leading the industry in its transformation toward a low-carbon future.
Comments